Introducción
The relentless demand for reliable electricity in our increasingly urbanized and industrialized world necessitates efficient and robust power distribution networks. Operating at the crucial medium-voltage level, 11 kilovolt (11kV) systems form the backbone of power distribution in numerous countries, including significant parts of Asia, the UK, and elsewhere. Bridging the gap between higher voltage transmission lines and low-voltage end-users requires dependable and strategically located substations. While traditional open-air substations have served this purpose for decades, the constraints of modern environments – limited space, aesthetic concerns, rapid deployment needs, and heightened safety requirements – have driven the widespread adoption of 11kV Compact Substations (CSS), also known as Packaged Substations (PSS) or Unitized Substations (USS).
These engineered assemblies represent a significant evolution in substation design, integrating key components into a single, type-tested, factory-built unit. But what exactly constitutes an 11kV CSS, where are they best applied, and what factors govern their selection? This article provides a comprehensive exploration for engineers, system designers, and technical specifiers navigating the world of modern medium-voltage distribution.
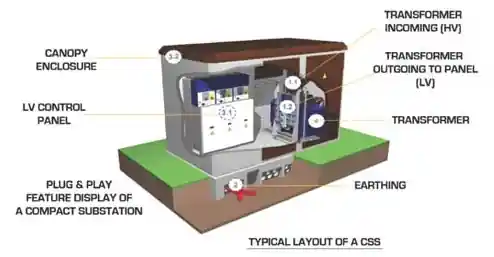
What is a Compact Substation (CSS)? The Core Concept
A Compact Substation is essentially a self-contained electrical substation assembly, prefabricated and tested in a factory environment before being transported to the site for installation. Unlike conventional substations, which involve assembling individual components (transformers, switchgear, control panels) on-site within a fenced-off area often requiring significant civil works, a CSS integrates these elements into optimized compartments within a common, typically metallic, enclosure.
Specifically for an 11kV Compact Substation, the primary function is to receive electrical power at the 11kV medium voltage (MV) level, transform it down to a usable low voltage (LV) – commonly 400V, 415V, or similar three-phase voltages (like the 380V/220V system often derived downstream in Taiwan, though 415V/240V is a common direct LV output globally) – and distribute this LV power through integrated switchgear. The key characteristic is this integration within a single, compact, and enclosed unit.
This design philosophy shift offers numerous advantages, moving much of the complex assembly and testing work from the field into a controlled factory environment, significantly impacting project timelines and quality assurance. As defined loosely by standards related to high-voltage switchgear assemblies like IEC 62271-202, these units are considered type-tested assemblies, ensuring a high degree of reliability and safety.
Key Components of an 11kV Compact Substation
While designs vary between manufacturers (such as ABB, Schneider Electric, Siemens, Eaton, and numerous regional players), a typical 11kV CSS comprises three main functional compartments housed within a shared enclosure:
- Medium Voltage (MV) Switchgear Compartment (11kV Side): This section houses the equipment for connecting to the incoming 11kV supply and providing switching and protection. Common configurations include:
- Ring Main Unit (RMU): A very common choice, particularly for distribution networks. RMUs typically contain load break switches (for incoming/outgoing feeders in a ring system) and a fused switch or circuit breaker for transformer protection. They offer a compact, often gas-insulated (SF6 or alternatives), and safe method for MV switching.
- MV Switchgear Panels: In some larger CSS or specific application designs, standalone MV switchgear panels with circuit breakers (vacuum or SF6) might be used, offering higher capabilities but potentially increasing the footprint.
- Protection: Overcurrent and earth fault protection is provided either by fuses (often combined with load break switches) or by relays operating MV circuit breakers.
- Transformer Compartment: This houses the power transformer responsible for stepping down the voltage from 11kV to the required LV level. Key considerations include:
- Type: Can be either oil-immersed (ONAN/ONAF cooling) or dry-type (AN/AF cooling, using cast resin or vacuum pressure impregnation). Dry-type transformers are often preferred for indoor or environmentally sensitive locations due to lower fire risk and no oil leakage potential.
- Rating: Typically ranges from around 100 kVA up to 2500 kVA or even higher for 11kV distribution applications, depending on the load requirements.
- Vector Group & Impedance: Standardized parameters critical for parallel operation and fault level calculations.
- Low Voltage (LV) Switchgear Compartment (e.g., 415V/240V Side): This section contains the LV distribution board for controlling and protecting outgoing LV feeders. It typically includes:
- Main Incoming Breaker: An Air Circuit Breaker (ACB) or Moulded Case Circuit Breaker (MCCB) connected to the transformer’s LV terminals.
- Outgoing Feeders: Multiple MCCBs or fuse units protecting individual LV circuits supplying loads.
- Instrumentation & Metering: Voltage/current meters, energy meters (as required by utility or facility).
- Barras conductoras: Copper or aluminum busbars distributing the LV power.
- Enclosure & Auxiliaries: The common housing providing protection and structural integrity.
- Material: Usually galvanized sheet steel with durable paint finish, though other materials like GRP (Glass Reinforced Polyester) are sometimes used.
- Protection Degree: Rated according to IEC 60529 (e.g., IP54 or IP55) to protect against dust ingress and water spray, ensuring suitability for outdoor installation.
- Ventilation: Natural or forced ventilation systems are crucial, especially for the transformer compartment, to manage heat dissipation.
- Interlocking & Safety Features: Mechanical and sometimes electrical interlocks prevent unsafe operations (e.g., accessing the MV compartment while live). Earthing provisions are critical.
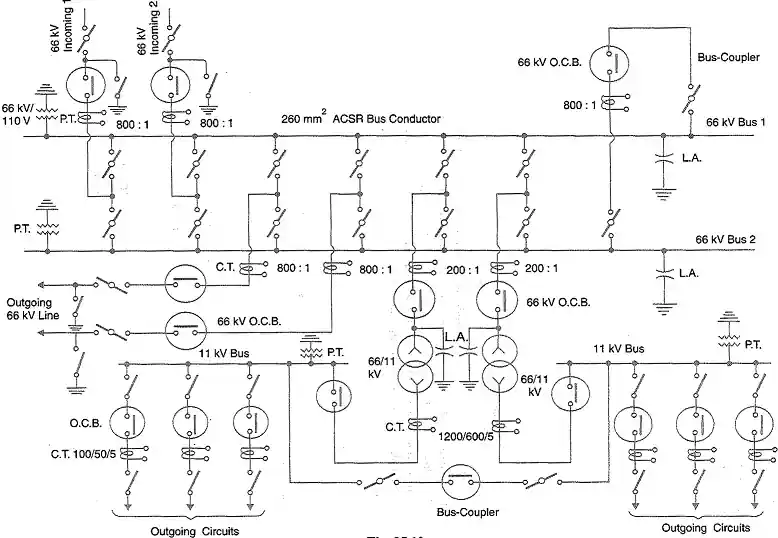
Advantages of Utilizing 11kV Compact Substations
The integrated and prefabricated nature of 11kV CSS offers compelling advantages over traditional substation construction:
- Significant Space Savings: Their compact footprint is ideal for densely populated urban areas, industrial sites with limited space, or underground installations. They require considerably less land area compared to open-air substations.
- Reduced Installation Time & Cost: Being factory-built and tested, on-site work is minimized primarily to civil foundation preparation, cable connections, and commissioning. This drastically reduces project schedules and associated labor costs.
- Mayor seguridad: The enclosed, metallic design with built-in safety interlocks provides superior protection for personnel compared to open-air installations. Access to live parts is restricted, reducing the risk of accidental contact. Conformance to standards like IEC 62271-202 ensures arc-fault containment capabilities in many designs.
- Improved Aesthetics & Lower Environmental Impact: The enclosed design is visually less intrusive than open-air substations, blending better into urban or sensitive landscapes. Reduced civil works also minimize site disruption.
- Plug-and-Play Nature: The integrated unit simplifies design and procurement. Once delivered, it requires mainly external connections.
- High Reliability: Factory assembly under controlled conditions generally leads to higher build quality and reliability compared to field assembly. Type-testing validates the design’s performance under various conditions.
- Flexibility: Standardized designs allow for easier replication, while modular concepts offer some degree of customization and potential future expansion or relocation, particularly for skid-mounted versions.
Where are 11kV Compact Substations Applied?
The versatility and advantages of 11kV CSS make them suitable for a wide array of applications:
- Urban and Residential Distribution: Powering apartment complexes, housing developments, and neighborhoods where space is at a premium and aesthetics matter.
- Instalaciones industriales: Providing reliable power to factories, processing plants, manufacturing units, often requiring dedicated, localized power transformation.
- Commercial Sector: Essential for large buildings like shopping malls, office towers, hotels, hospitals, and data centers that have significant power demands.
- Infrastructure Projects: Supplying power for airports, railway systems (traction and signaling), ports, and tunnels.
- Renewable Energy Integration: Connecting solar farms (PV plants) and wind farms to the 11kV distribution grid, often requiring outdoor, robust solutions. The compact nature is advantageous in remote or space-constrained renewable sites.
- Temporary Power Supply: Used for large construction sites, events, or emergency power restoration scenarios due to their relatively quick deployment.
Market Trends and Development Context
The demand for 11kV compact substations is steadily growing, driven by several interconnected global and regional trends:
- Rapid Urbanization: Continuous growth of cities worldwide necessitates space-efficient infrastructure, making CSS the preferred solution for new urban developments.
- Grid Modernization: Utilities are upgrading aging infrastructure. CSS fits well into smart grid concepts, often incorporating communication interfaces for remote monitoring and control (SCADA integration).
- Distributed Generation: The surge in renewable energy sources (RES) requires numerous distributed grid connection points. CSS provides a standardized and efficient interface between RES installations and the MV distribution network. Taiwan’s strong commitment to renewable energy, for example, fuels demand for such grid connection solutions.
- Focus on Safety & Reliability: Increasingly stringent safety regulations and the high cost of outages push industries and utilities towards inherently safer, factory-tested solutions like CSS. Standards organizations like IEC and IEEE continually refine guidelines (e.g., IEC 62271-202 for Prefabricated Substation Assemblies) reflecting best practices.
- Cost-Effectiveness: While the initial unit cost might seem higher than unassembled components, the savings in land, civil works, installation time, and potentially reduced maintenance often result in a lower total cost of ownership. Industry bodies and market reports often highlight the growing market share of prefabricated electrical infrastructure.
Key Technical Parameters & Specifications
When specifying or evaluating an 11kV CSS, engineers must consider several critical parameters:
- Rated Primary Voltage: 11kV (aligning with the MV network).
- Rated Secondary Voltage: e.g., 400V, 415V, 380V/220V (depending on local standards and application).
- Rated Power (kVA): Determined by the maximum load demand, considering diversity and future growth. Standard ratings might range from 160kVA to 2500kVA or more.
- Frecuencia nominal: 50 Hz or 60 Hz (Taiwan operates at 60Hz).
- MV Switchgear:
- Type: RMU (SF6/Air/Solid Insulated), Disconnector Switches with Fuses, Circuit Breaker (Vacuum/SF6).
- Rated Short-Time Withstand Current & Duration (e.g., 16kA or 20kA for 1 sec).
- Rated Peak Withstand Current.
- Rated Interrupting Current (for circuit breakers/fused switches).
- LV Switchgear:
- Configuration: Number and rating (Amperes) of outgoing feeders (MCCBs/fuses).
- Main Incomer Rating (ACB/MCCB).
- Short-Circuit Withstand Rating (kA).
- Transformer: Type (Oil/Dry), kVA Rating, Cooling (ONAN/AN), Vector Group (e.g., Dyn11), Percentage Impedance (%Z).
- Insulation Levels (BIL): Basic Impulse Level ratings for MV and LV sides (e.g., 75kV BIL for 11kV equipment).
- Degree of Protection (IP Rating): E.g., IP54 indicates protection against dust ingress and water spray from all directions. Higher ratings may be needed for harsh environments.
- Applicable Standards: Compliance with relevant international (IEC 62271-202) and potentially local standards (like specific CNS standards or Taipower requirements in Taiwan) is crucial.
Comparison: Compact Substations vs. Conventional Substations
Característica | 11kV Compact Substation (CSS) | Conventional 11kV Substation |
---|---|---|
Footprint | Very Small, Optimized | Large, requires significant land area |
Installation Time | Short (days/weeks) | Long (weeks/months) |
Civil Works | Minimal (foundation pad) | Extensive (foundations, structures, fence) |
Cost | Lower lifecycle cost often, higher initial unit | Lower component cost, higher overall project |
Safety | High (Enclosed, Interlocked, Type-Tested) | Moderate (Open-air, requires strict access) |
Environmental | Low Visual Impact, Less Site Disruption | Higher Visual Impact, More Site Work |
Flexibility | High (Standardized, Potentially Relocatable) | Low (Fixed Installation) |
Maintenance | Generally easier access to integrated parts | Can require access across larger area |
导出到 Google 表格
Major manufacturers like Schneider Electric, ABB, and Siemens often provide detailed comparisons highlighting the total cost of ownership and deployment speed advantages of CSS solutions in suitable applications.
Selection Guidance for 11kV Compact Substations
Choosing the right 11kV CSS requires careful consideration of project-specific needs:
- Define Load Requirements: Accurately determine the present and future kVA demand to size the transformer correctly.
- Analyze MV Network Interface: Is it a ring or radial feed? This dictates the required RMU configuration (number of switches/breakers).
- Calculate Fault Levels: Determine the maximum prospective short-circuit current at the MV connection point. Ensure the CSS switchgear has an adequate interrupting rating and withstand capability.
- Assess Environmental Conditions: Consider ambient temperature range, altitude, humidity, seismic activity, and potential for corrosion. This influences enclosure material, IP rating, ventilation/cooling design, and potential derating factors.
- Evaluate Site Constraints: Factor in available space, access routes for delivery and maintenance, and any aesthetic requirements.
- Specify LV Distribution Needs: Determine the number, size, and protection requirements for outgoing LV feeders.
- Consider Automation & Monitoring: Does the CSS need to integrate with a SCADA system? Specify requirements for remote monitoring, control, and metering.
- Ensure Standards Compliance: Verify compliance with relevant international (IEC) and crucially, local utility standards and regulations (e.g., Taipower standards in Taiwan). This is non-negotiable for grid connection.
- Evaluate Manufacturers: Consider manufacturer reputation, track record, technical support, warranty, and availability of spare parts.
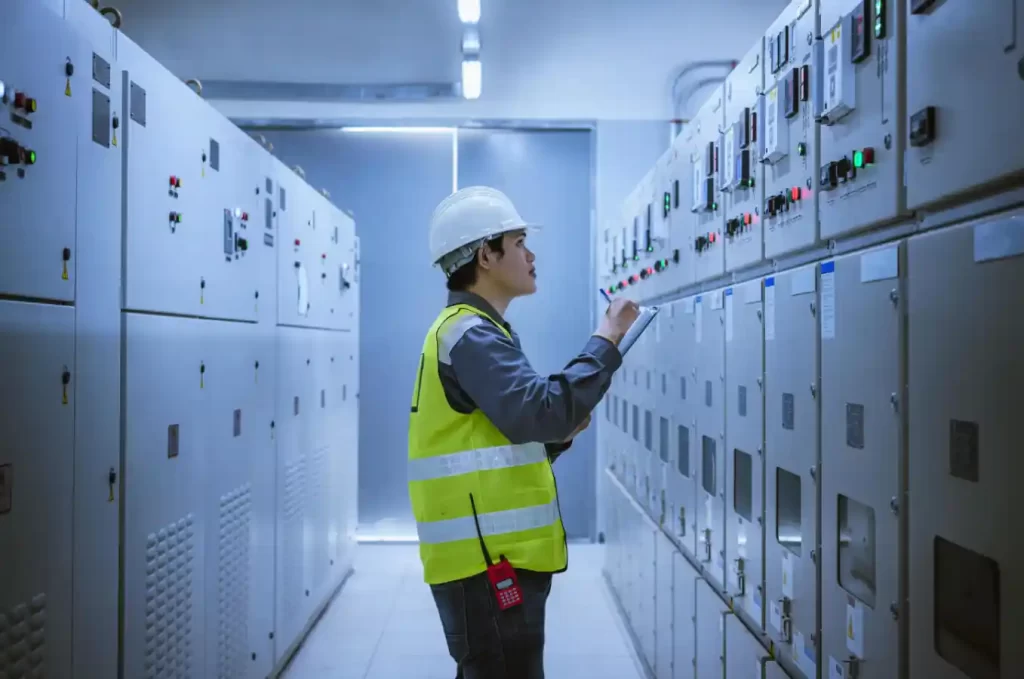
11kV compact substations have emerged as a cornerstone of modern electrical distribution infrastructure. Their integrated design, factory-built quality, enhanced safety features, and significantly reduced footprint and installation time offer compelling advantages over traditional construction methods, particularly in space-constrained or rapidly developing environments. From powering bustling city centers and industrial complexes to enabling the integration of renewable energy sources, 11kV CSS provides a reliable, efficient, and increasingly sophisticated solution for stepping down power closer to the end-user. Careful consideration of load requirements, system parameters, fault levels, environmental conditions, and adherence to both international and local standards, as outlined in this guide, is key to successfully selecting and deploying these vital components of our electrical future.
Preguntas más frecuentes (FAQ)
A: The operational lifespan of an 11kV CSS typically ranges from 25 to 30 years or more, depending heavily on factors such as the quality of components (transformer, switchgear), adherence to a proper maintenance schedule, environmental conditions (temperature, humidity, pollution levels), and the operational load profile. Key components like the transformer and MV switchgear often dictate the overall lifespan. Regular preventive maintenance significantly contributes to longevity.
A: Yes, compact substations can be specified for corrosive environments, but require careful consideration during the design and selection phase.
Options include:
Enclosure Material: Using higher-grade stainless steel or GRP (Glass Reinforced Polyester) instead of standard galvanized steel.
Protective Coatings: Applying specialized multi-layer paint systems resistant to salt spray or chemical fumes.
Higher IP Rating: Specifying a higher Degree of Protection (e.g., IP55 or IP56) to better seal against corrosive dust and moisture ingress.
Component Selection: Ensuring internal components are also suitably rated or protected for the environment. It’s crucial to discuss these requirements explicitly with the manufacturer.
A: Routine maintenance is essential for ensuring reliability and longevity. Typical tasks, often performed annually or biannually based on manufacturer recommendations and site conditions, include:
Visual Inspection: Checking the enclosure for damage, corrosion, water ingress; inspecting visible components, seals, and labels.
Cleaning: Removing dust and debris, especially around ventilation openings.
Thermal Imaging (Thermography): Scanning connections, busbars, and components for hotspots indicating poor connections or overloading.
MV/LV Switchgear Checks: Functional testing of switches/breakers (if possible/required), checking protection relay settings, inspecting contacts (where accessible).
Transformer Maintenance: For oil-immersed types, checking oil level, temperature, pressure relief device, and potentially taking oil samples for Dissolved Gas Analysis (DGA). For dry-types, checking winding cleanliness and temperature monitoring systems.
Earthing System Check: Verifying the integrity of the main earthing connections.
Documentation Review: Keeping maintenance logs updated.
Get a printable version of this page as a PDF.