In the realm of power power distribution and grid stability, the high voltage compensation cabinet plays a critical role in improving power factor, reducing losses, and ensuring stable voltage levels across industrial and utility applications. These cabinets are widely installed in medium to high-voltage networks, where they serve to compensate for reactive power and enhance overall power quality.
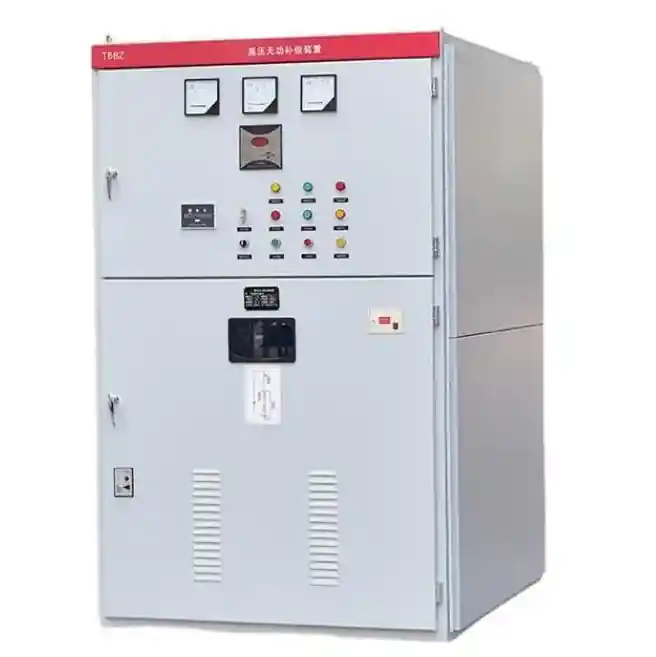
Key Functions and Benefits
The primary function of a high voltage compensation cabinet is to provide reactive power compensation. By dynamically adjusting the reactive load, it ensures that power factor remains within desirable levels (usually close to 1), thereby reducing energy losses, avoiding penalties from utilities, and prolonging equipment lifespan.
Benefits include:
- Improved voltage stability in distribution networks
- Reduced energy losses and enhanced efficiency
- Lower maintenance costs due to reduced equipment stress
- Compliance with grid code and power quality standards
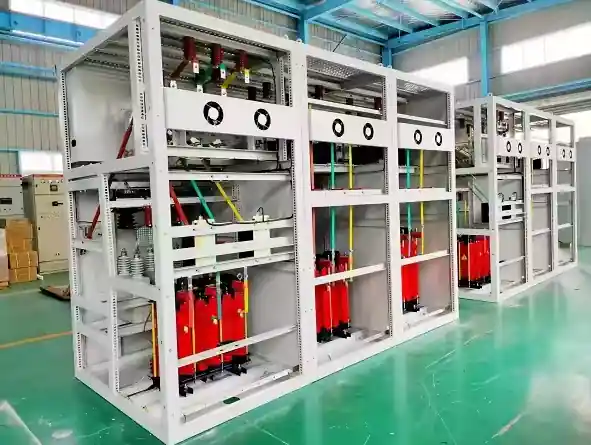
Typical Structure and Components
A standard high voltage compensation cabinet consists of the following core components:
- High-voltage capacitors: Provide the reactive power needed for compensation
- Reactors: Limit inrush current and suppress harmonics
- Vacuum contactors: Enable safe switching of capacitor banks
- Discharge resistors: Ensure safety during shutdown
- Protection relays: Monitor voltage/current and trip during faults
- Control systems: Automatic adjustment based on real-time power factor readings
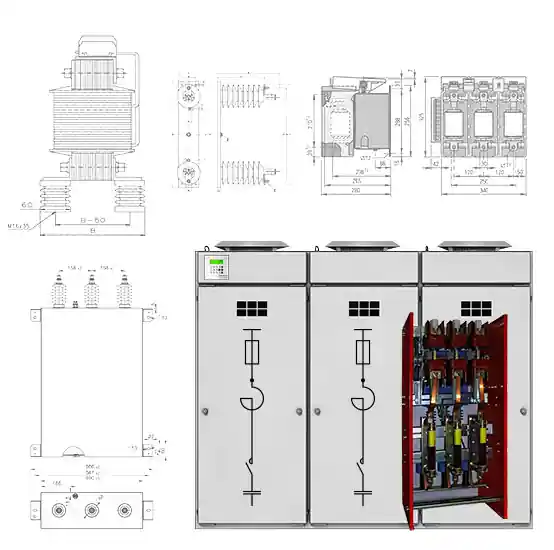
Technical Specifications
While configurations vary, a typical high voltage compensation cabinet may include:
- Rated Voltage: 6kV / 10kV / 35kV
- Rated Frequency: 50Hz / 60Hz
- Compensation Capacity: Ranges from 100kvar to 5000kvar
- Protection Class: IP30~IP54
- Switching Method: Manual / Automatic / Thyristor-controlled
- Ambient Conditions: Operating temp -25℃ ~ +45℃, relative humidity ≤ 95%
Applications and Usage Scenarios
High voltage compensation cabinets are extensively used in:
- Industrial manufacturing plants with heavy machinery
- Steel mills, mines, and chemical processing units
- Substations and power distribution centers
- Renewable energy integration sites where load variation is high
These cabinets are essential in places where maintaining power quality is critical for operational continuity.
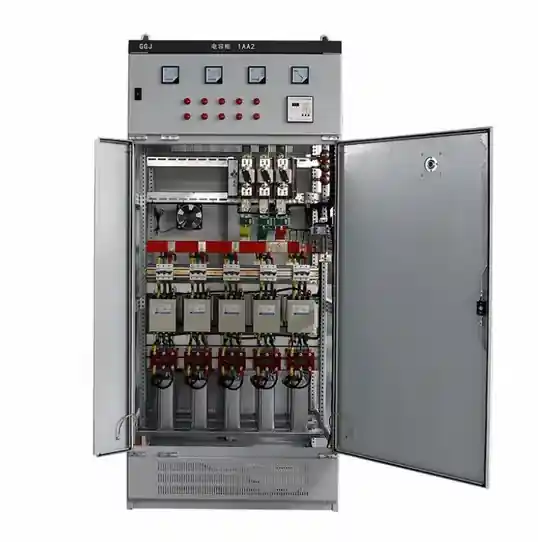
Selection Guide and Maintenance Tips
When selecting a high voltage compensation cabinet, users should consider:
- Grid voltage and compensation capacity required
- Load nature: continuous or fluctuating
- Harmonic levels: determine if filters are needed
- Control method preference: fixed step vs. automatic compensation
For maintenance:
- Inspect capacitor swelling or leakage regularly
- Check contactor condition and thermal relays
- Ensure cooling and ventilation systems are functioning
- Test insulation resistance periodically
FAQs
Q1: What is the difference between low voltage and high voltage compensation cabinets?
A: Low voltage cabinets operate at ≤1kV, suitable for commercial buildings, while high voltage cabinets handle 6kV–35kV and are used in industrial/power systems.
Q2: Can these cabinets operate in environments with high harmonics?
A: Yes, but it is recommended to use detuned reactors or harmonic filters to prevent resonance.
Q3: How does automatic compensation work?
A: The control unit continuously monitors the system power factor and automatically switches capacitor groups to maintain it at an optimal level.